APQP: כלי לניהול פרויקטים להבטחת איכות פרואקטיבית
APQP (Advanced Product Quality Planning) נולד בשנות ה-80 בתעשיית הרכב האמריקאית, כאשר יצרניות כמו פורד, ג'נרל מוטורס וקרייזלר התמודדו עם תחרות עזה מיצרנים יפנים. הכלי פותח כדי לשפר את האיכות והעקביות של המוצרים ולספק יתרון תחרותי. כיום, APQP הפך לכלי מרכזי בתעשיות האווירונאוטיקה, החלל והביטחון, המיושם על פי תקן IAQG 9145.
מעבר מתגובות לבעיות לתכנון מובנה ואסטרטגי
בעולם שבו איכות ואמינות הן דרישות בסיסיות, APQP מאפשר לתעשיות אלו לזהות בעיות מראש, לפני שהן משפיעות על תהליך הייצור. הכלי מעודד מעבר מתגובות לבעיות שהתגלו לתכנון מבוסס סיכונים, שמטרתו להבטיח יציבות ועמידה בדרישות לאורך זמן.
שורשי APQP: ממכוניות לחלל
APQP החל כתשובה לאתגרים בתעשיית הרכב, כאשר הסטנדרט החדש שנוצר סייע לשפר את איכות המוצרים ואת שיתוף הפעולה עם ספקים. עם הזמן, הצלחת המודל הביאה לאימוצו בתעשיות נוספות, כמו רפואה וממשל. כיום, תקן IAQG 9145 מתאים את השיטה לצרכים המורכבים של תעשיות האווירונאוטיקה והביטחון.
טיפ פרקטי: למדו את ההיסטוריה של APQP בתעשיות דומות כדי להפיק לקחים ולשפר את תהליכי האיכות בארגון שלכם.
היסודות והיתרונות של APQP
בבסיס APQP עומדים שיתוף פעולה בין תחומים, זיהוי מוקדם של סיכונים ותכנון איכותי פרואקטיבי.
היתרונות הבולטים כוללים:
- זיהוי מוקדם של תקלות: מבנה התהליך מאפשר לטפל בבעיות עוד בשלבי הפיתוח המוקדמים.
- שיתוף פעולה בין-תחומי: פירוק מחסומים ארגוניים מעודד תקשורת פתוחה ושיפור עבודה צוותית.
- שיפור בביצועי ספקים: הנחיות ברורות מסייעות לספקים לעמוד בדרישות האיכות.
- שביעות רצון לקוחות: עמידה בציפיות הלקוח באמצעות מסגרת איכותית מובנית מגבירה אמון.
סטטיסטיקה חשובה: חברות המיישמות APQP מדווחות על ירידה משמעותית במקרי חוסר ההתאמה בתהליכי ייצור.
שלבים מרכזיים ב-APQP
APQP פועל במתודולוגיה של חמישה שלבים, בהם מטופלים סיכונים בשלבים שונים של פיתוח המוצר:
- תכנון: איסוף דרישות, הגדרת היקף הפרויקט וקביעת מטרות.
- פיתוח מוצר: ניתוח סיכוני תכנון (DFMEA) והטמעת אמצעי מנע.
- פיתוח תהליך: יישום PFMEA ותוכניות בקרה לשמירה על יציבות הייצור.
- אימות מוצר ותהליך: ביצוע בדיקות ראשונות להבטחת עמידה בתקני איכות.
- ייצור מתמשך ושיפור מתמיד: הטמעת לקחים לשיפור תהליכים וייצור שוטף.
טיפ פרקטי: בנו תהליך עבודה ברור לכל שלב כדי למנוע טעויות ולשפר את היעילות.
תפקיד ה-PPAP בשמירה על עקביות
Production Part Approval Process (PPAP) הוא חלק אינטגרלי מ-APQP, המסייע להבטיח שייצור המוצרים עומד בדרישות באופן עקבי. תהליך זה כולל סקירת אלמנטים מרכזיים כמו DFMEA ו-PFMEA לקביעת קו בסיס איכותי.
ציטוט רלוונטי: "האיכות אינה מתרחשת במקרה; היא תוצאה של מאמצים שיטתיים." – ג'ון וודן
שיפורים בתקן 9145 החדש
גרסה חדשה של תקן IAQG 9145 נמצאת בתהליכי עדכון ותשפר את ההפרדה בין דרישות מחייבות לאלמנטים אופציונליים, כמו גם את ההנחיות לניהול שינויים.
טיפ פרקטי: עקבו אחר עדכוני התקן כדי לשלב את החידושים במהירות בתהליכי העבודה שלכם.
משאבים ותמיכה ליישום APQP
IAQG מציעה מגוון משאבים ייעודיים ב-SCMH (Supply Chain Management Handbook) הכוללים הדרכות, תבניות וכלים להטמעת APQP.
מסר מסכם: אימוץ APQP מאפשר לתעשיות האווירונאוטיקה והביטחון להתקדם לעתיד שבו תכנון איכותי הוא חלק בלתי נפרד מכל שלב בפיתוח וייצור. גישה זו מבטיחה עמידות, אמינות ומצוינות.
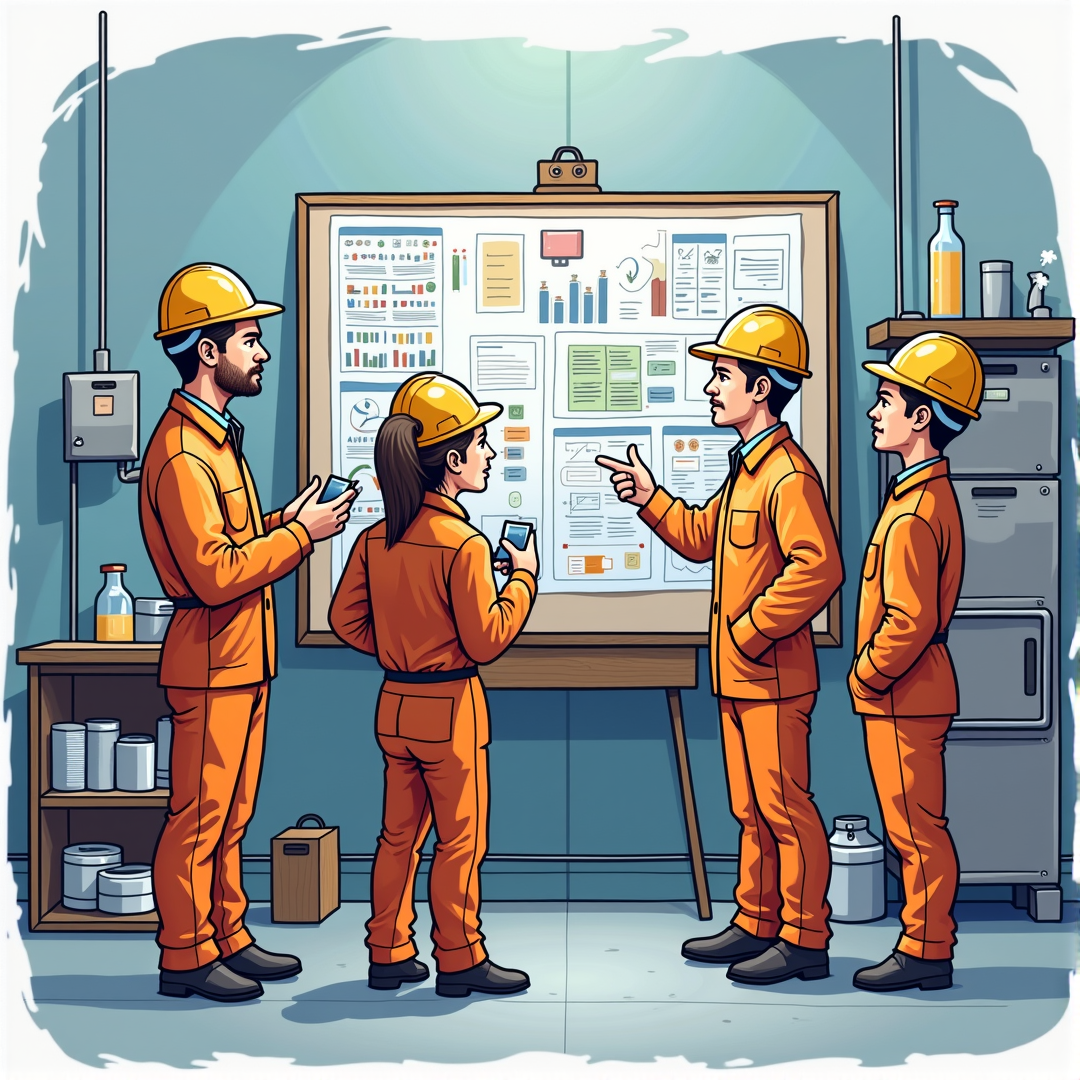
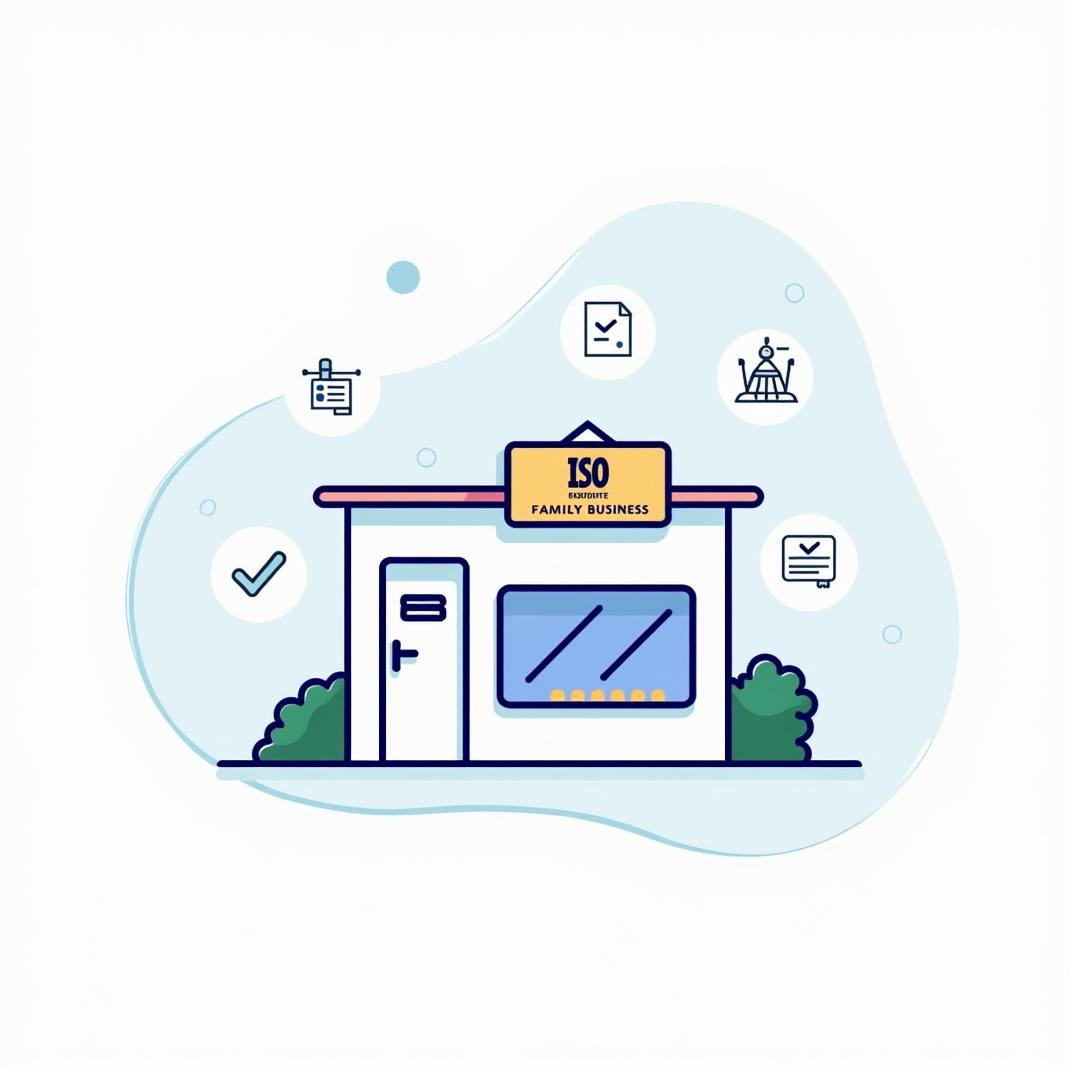
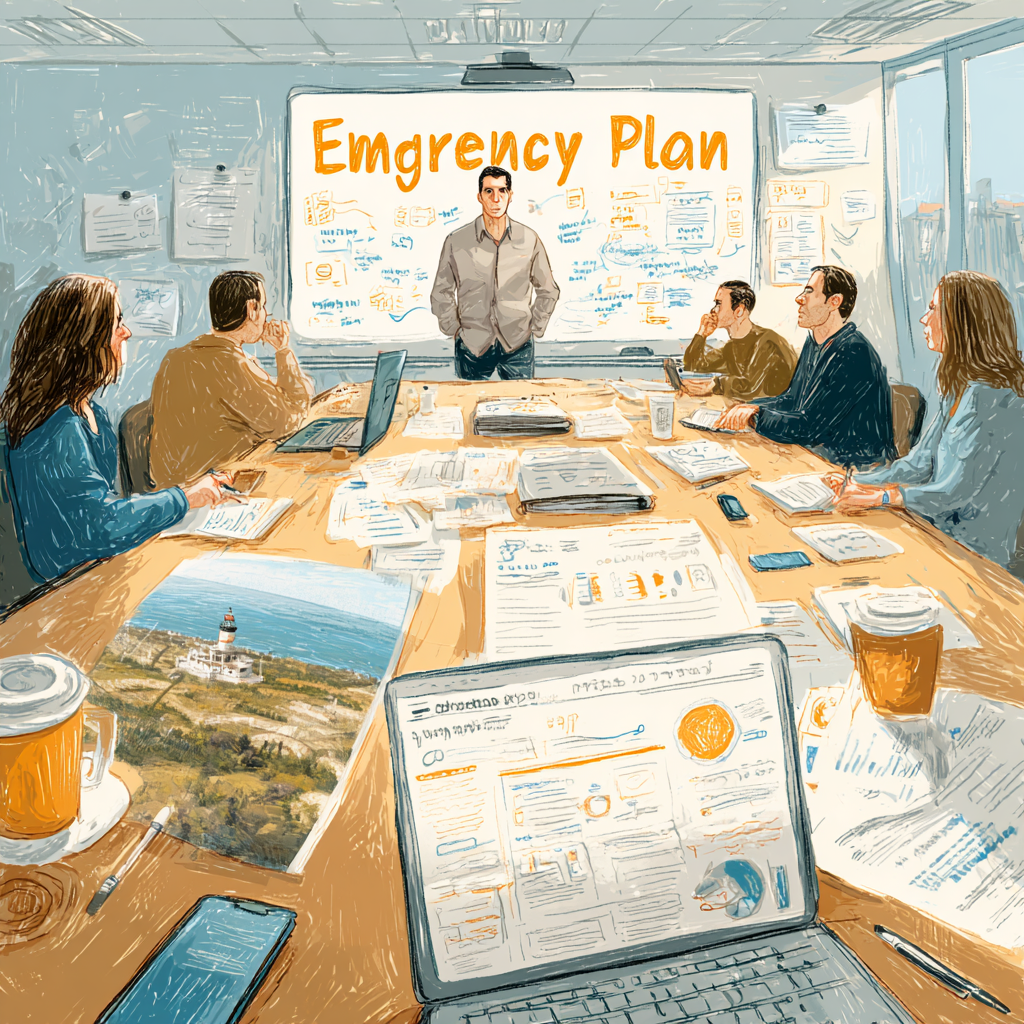